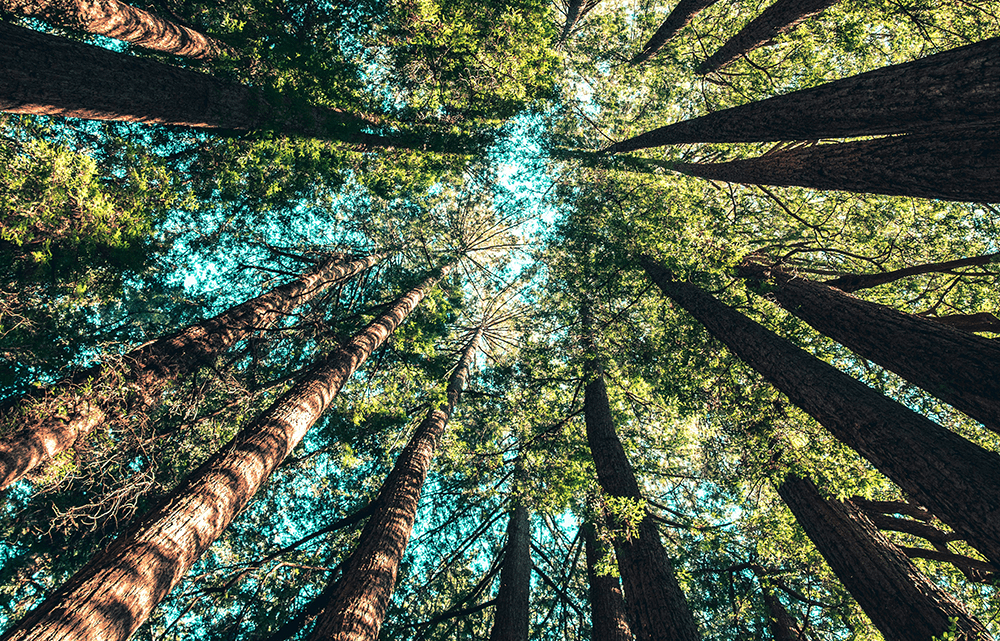
PAPER MANUFACTURING
Raw Materials
After having been a traditional craft activity for a long time, today’s paper manufacturing is more sophisticated, while respecting tradition.
Paper is essentially a mixture of fibres from various plants. Early paper was manufactured using textiles such as linen, hemp, then cotton. However, these materials are costly and there are insufficient quantities given the considerable increase in production. In 1719, François Réaumur was supposedly the first to think of making paper with wood, inspired by wasps making their nests with chewed up, kneaded paper. Today rolling paper is made with a variety of textiles or wood fibers. The plant materials ZIG-ZAG selects for its papers are chosen for their resistance and thinness, with total respect for nature. The woods used by Zig-Zag come from forests that are sustainably managed. They are carefully selected for their strong and resistant fibers. These materials meet very strict criteria such as those set by FSC certification. Textile plants come from linen and flax that are planted every year. They add flexibility and thinness to the paper.
PAPER MANUFACTURING
Manufacture, And Pulp Preparation
To make pulp, the pieces of word are cooked to soften them, then they are scraped with huge grindstones called defibrators, which tear away the fibres or clumps of fibres. This is a long mechanical process with gradually breaks vegetal matter down into small fibres.
These fibres are then cleaned at high temperatures and compacted at high pressures. The fibre balls obtained are then poured into a large vat called a pulper, to separate the fibres in a large quantity of water. This is the final preparation before making paper.
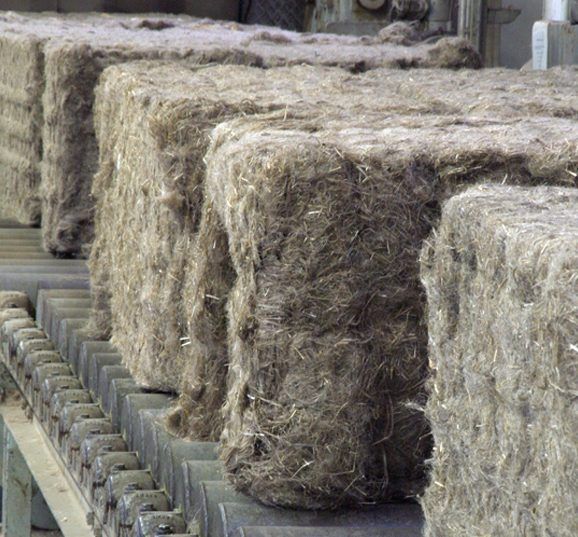
PAPER MANUFACTURING
The Gum
Our gum is therefore a completely natural product
It is very important to control the quantity and quality of the gum, for it ensures the cigarette is perfectly held together. The quality of the gum on ZIG-ZAG papers is known for its effectiveness.
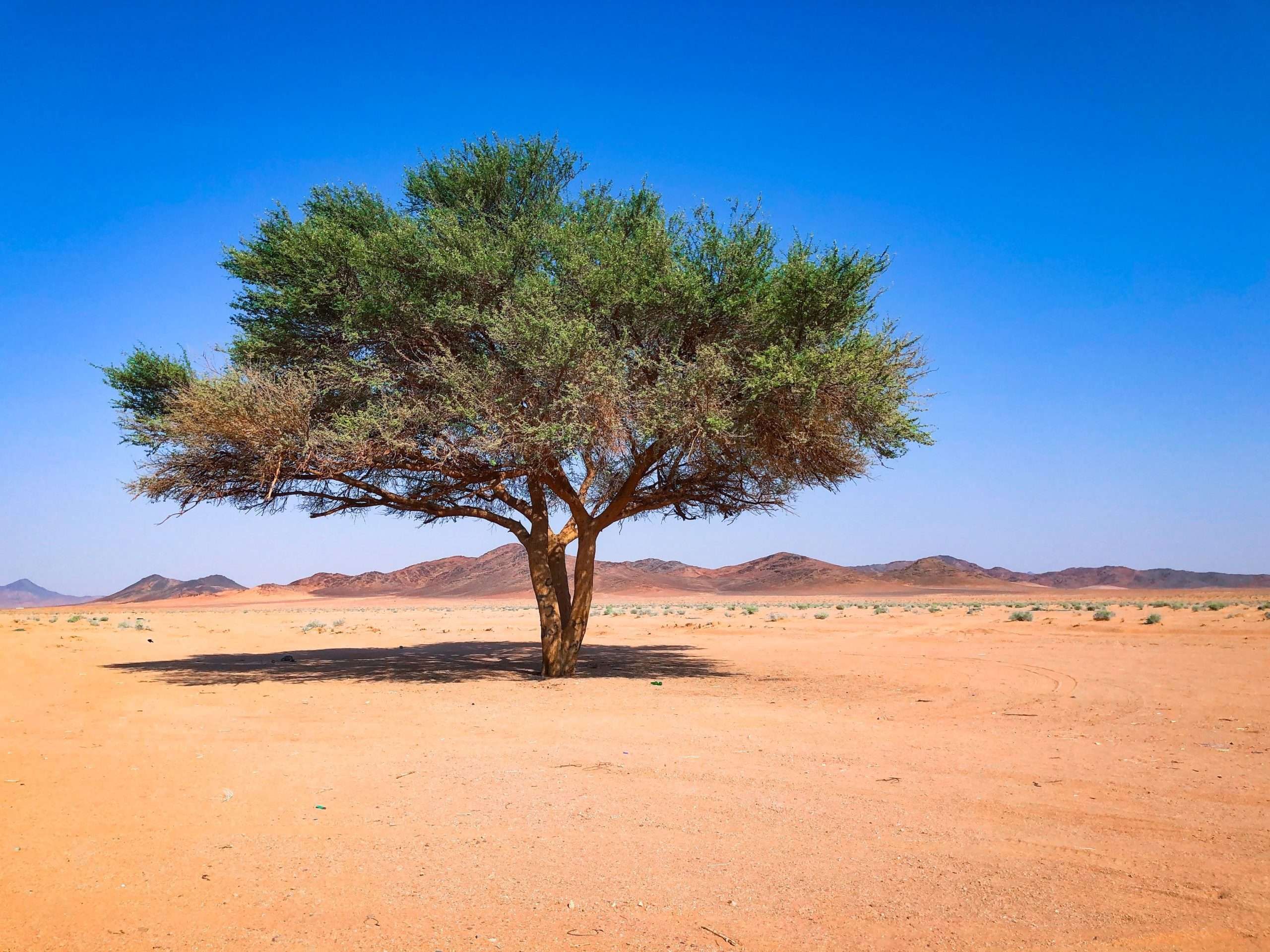
PAPER MANUFACTURING
Sheet Formation On Machine
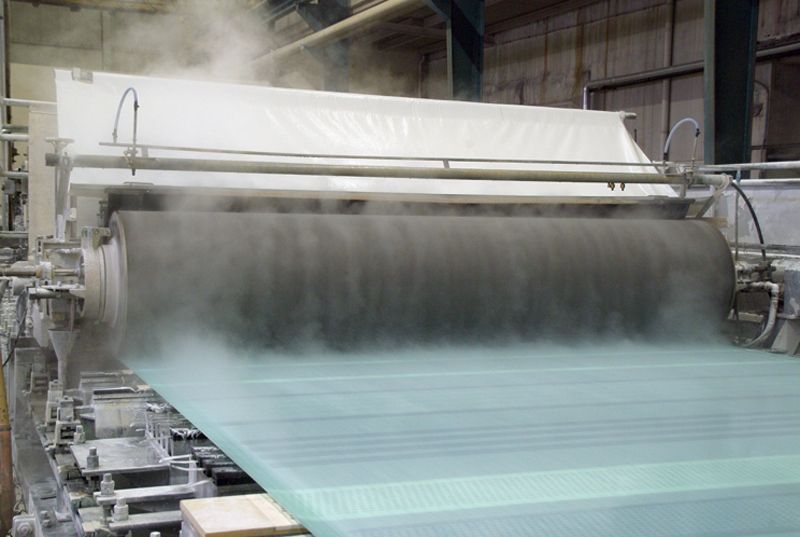
The pulp which arrives at the machine is a highly diluted fibre suspension. It only contains a few grammes of “dry materials” per litre, and is around 99.5% water.
The pulp is sprayed onto a large canvas (the forming table). As the sheet moves forward the fibres align themselves in the direction of the movement of the jet and will become interleaved to form a sheet.
Thanks to the lateral, jerking movement of the canvas, the sheet will have an even consistence and a large quantity of water will be drained away.
The sheet will then go into a long circuit of presses and heated cylinders, used to compress and finish drying the sheet.
There are many automatic checks which make it possible to continually adjust each parameter during production : flow, concentration, temperature, pressure, speed etc.
Automation is key as it brings reliability and consistency in quality.
On leaving the machine the sheet is rolled up: the original reel is unrolled and cut up to form reels whose size is adjusted for their end use. Each reel of paper weighs around 250 kg and is 25km long!
BOOKLET MANUFACTURING
1st Stage: Watermarking
he paper is made more transparent and stamped with the ZIG-ZAG pattern : This is called watermarking
To become a real ZIG-ZAG booklet, the paper undergoes several transformations. Watermarking adds the ZIG-ZAG pattern and logo. The watermarking machine unrolls the paper and puts it under high pressure in a roller engraved with the patterns you can see on the papers. The very complex operation enhances the transparency and thinness of the paper, a sign of quality. “Laid papers”, white, thicker and showing regular lines, are not watermarked. The stripes are marked during the initial paper-making process.
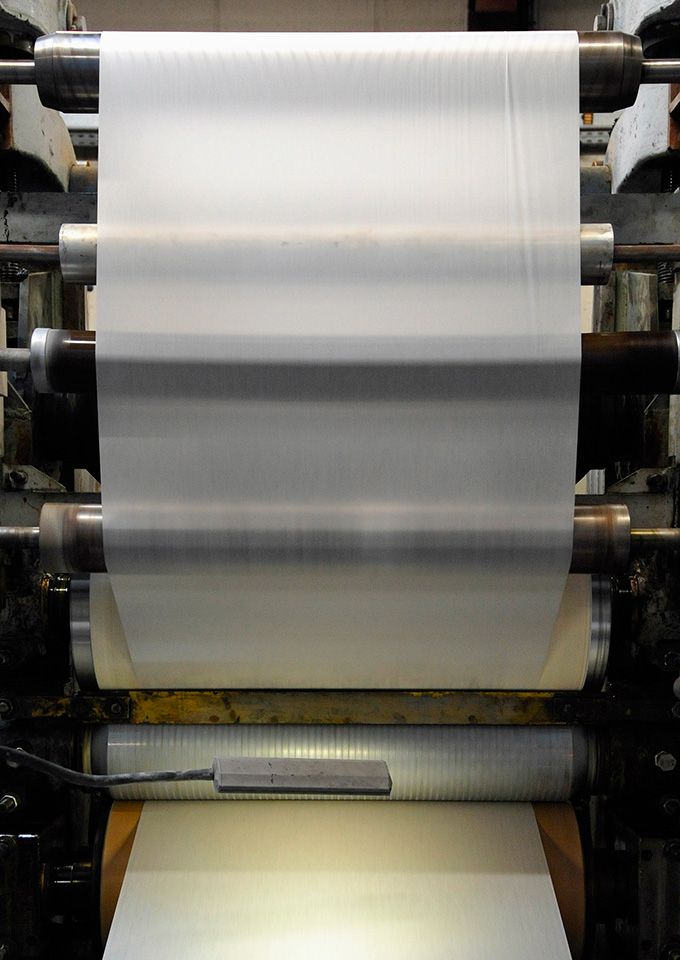
BOOKLET MANUFACTURING
2d Stage : The Gumming
Adding gum to the paper: The gumming.
The reels are cut to be around 100cm wide and fit in the gumming machine. This machine unrolls the reel and deposits several strips of natural acacia gum on it. The reel will be cut in the middle of each strip of gum and between each pair of strips. These are then rolled up into smaller reels, which now have the exact width of your paper and have the strip of gum on one side.
The gum used for Zig-Zag papers comes from the sap of acacia trees. It is extracted by making incisions into the trunks. It is mainly collected in Africa between December and June.
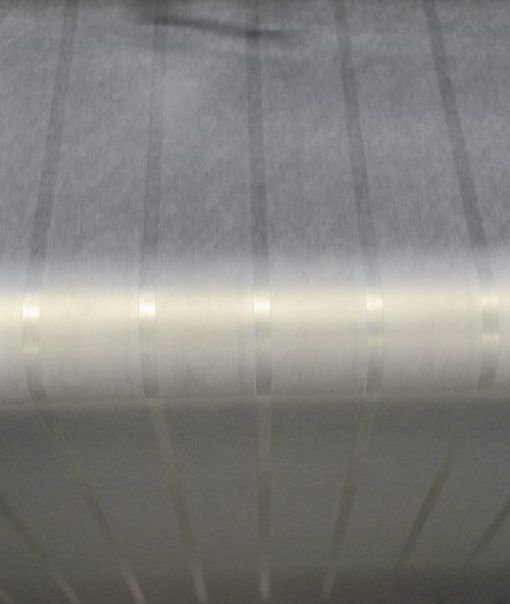
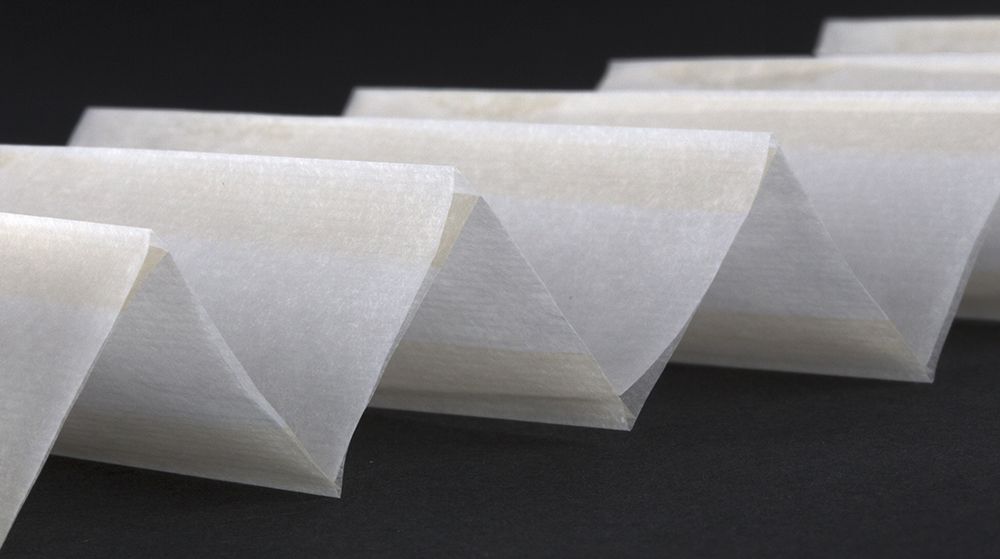
BOOKLET MANUFACTURING
3d Stage: Interleaving
The cut paper is then folded into blocks of leaves slotted into each other : interleaving.
The first interleaving machines unrolled reels and cut them to the length of the leaves in your booklet. During this cutting process, leaves were fed between two jagged wheels. When the wheels turn, the papers fold and become interleaved. Blocks of 50 leaves were thus formed for booklets of ZIG-ZAG Doubles.
These machines are the pride of ZIG-ZAG, whose founders, the Braunstein brothers, invented the process (see the history section). Nowadays new, more modern machines share production. These machines, which resemble large looms, interleave the reels constantly, then cut the folded paper into booklet format. For a block of 50 leaves, the machine unrolls 50 reels of gummed paper at once! As the paper of each reel moves forward, it is made to gradually bend in the middle. At the same time, 50 strips of paper progressively join together and pile up to form a giant fan, a kind of final crossroads, before being totally folded. Finally, the continuous flow of interleaved paper is cut to the length of the desired paper booklet.
Thanks to this assembly process, when you take out a paper, the next one comes up automatically. It is a complex and closely monitored operation.
BOOKLET MANUFACTURING
4th Stage : The Packing
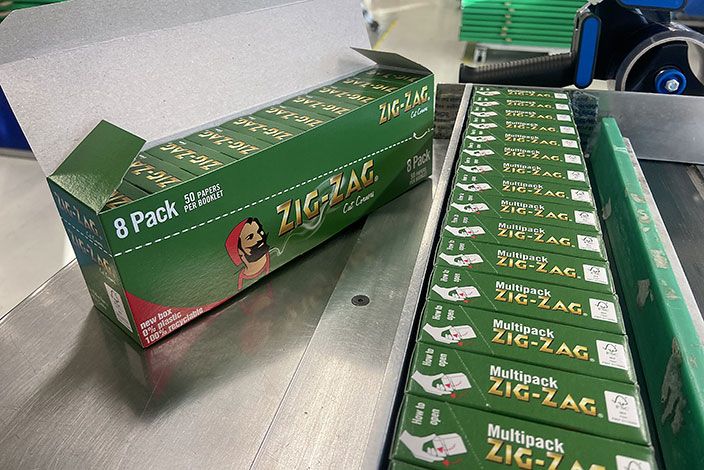
Blocks of paper are inserted into their cardboard covers: the packing.
The covers (cases) are placed flat onto the machine and move forward onto a conveyor to receive the blocks of interleaved papers. The cover flaps are then folded down. Finally, the finished booklets are placed into cases, then shipping boxes.
The boxes are ready to be sent to the despatch office, then on to the retailer and finally the smoker.